Table of Contents (click to expand)
The aluminum is first extracted from the bauxite ore and then smelted to produce pure aluminum metal.
Aluminum compounds have proven their usefulness for thousands of years. It has been around since the times of the Persian Empire, When Persian potters made their most robust vessels from clay that contained aluminum oxide. Ancient Egyptians and Babylonians used aluminum compounds in their fabric dyes, cosmetics and medicines. However, it was only in the early nineteenth century that aluminum was identified as an element and isolated as a pure metal. The difficulty of extracting aluminum from its natural compounds kept the metal rare for many years; half a century after its discovery, it was still as rare and valuable as silver. Now that we know a bit more about the history of the metal, let’s take a look at the properties of this metal and the raw materials needed to make aluminum.
Properties And Raw Materials
Aluminum is the third-most plentiful element in the earth’s crust, and it makes up 8% of the planet’s soil and rocks. In nature, aluminum is found only in chemical compounds with other elements, such as sulfur, silicon, and oxygen. The only place where aluminum can be extracted profitably is in the form of aluminum ores. Metallic aluminum has many properties, such as being lightweight, durable, nonmagnetic, and nontoxic. It conducts heat and electricity and reflects heat and light. It is stable, but easily workable, and it retains its strength under extreme cold without becoming brittle. The surface of aluminum quickly oxidizes to form an invisible barrier that prevents it from experiencing corrosion. Furthermore, aluminum can be produced efficiently and is economically recyclable for new products.
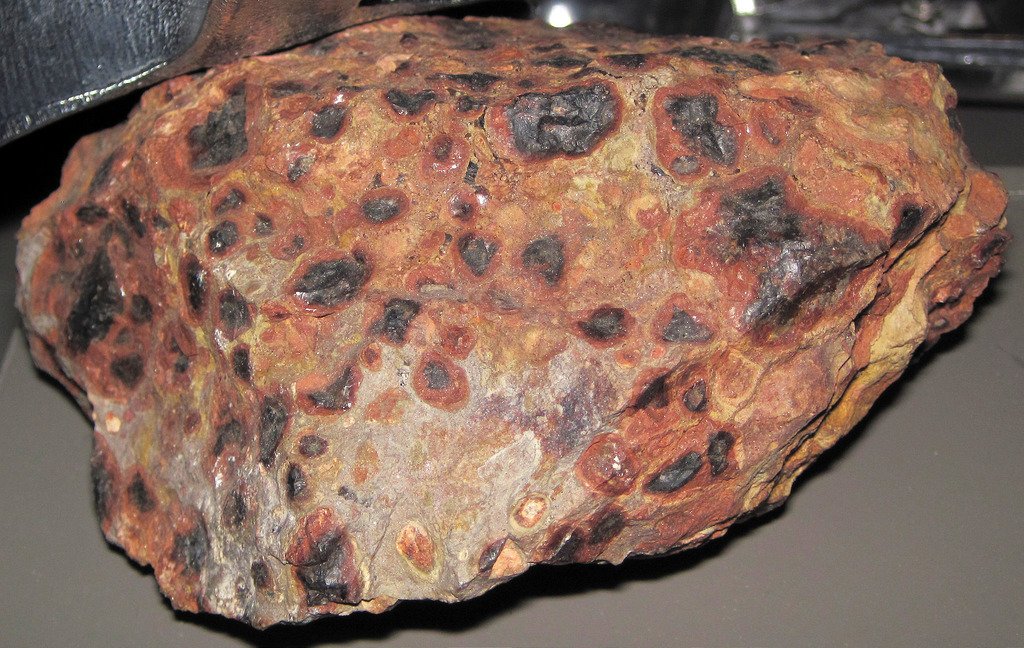
Aluminum compounds occur in all types of clay, but the ore that is most useful for producing pure aluminum is bauxite. Bauxite consists of 45-60% aluminum oxide, along with various impurities, such as sand, iron and other metals. Although some bauxite deposits are hard rock, most consist of relatively soft dirt that is easily dug out from open-pit mines. Australia produces more than one-third of the world’s supply of bauxite. It takes about 2 kg of bauxite to produce 0.5 kg of aluminum metal. Caustic soda (sodium hydroxide) is used to dissolve the aluminum compounds found in the bauxite, separating them from the impurities. Depending on the composition of the bauxite ore, relatively small amounts of other chemicals may be used in the extraction process. Aluminum is manufactured in two phases: The Bayer process of refining the bauxite ore to obtain aluminum oxide, and The Hall-Heroult process of smelting the aluminum oxide to release pure aluminum. Let’s take a closer look at these two methods.
Also Read: How Is Titanium Made?
Bayer Process
Initially, the bauxite ores are obtained and then crushed mechanically. The crushed ore is then mixed with caustic soda and put into a grinding mill, then made into a slurry containing the ore. The slurry is then pumped into the digester. The digester is a large tank that acts like a pressure cooker. The slurry is heated to 110-270°C at a pressure of 340 kPa. These conditions are maintained for a time ranging from half an hour to several hours. Additional caustic soda may be added to ensure that all aluminum-containing compounds are dissolved. The hot slurry, which has now become a sodium aluminate solution, passes through a series of flash tanks that reduce the pressure and recover heat, which can be reused in the refining process.
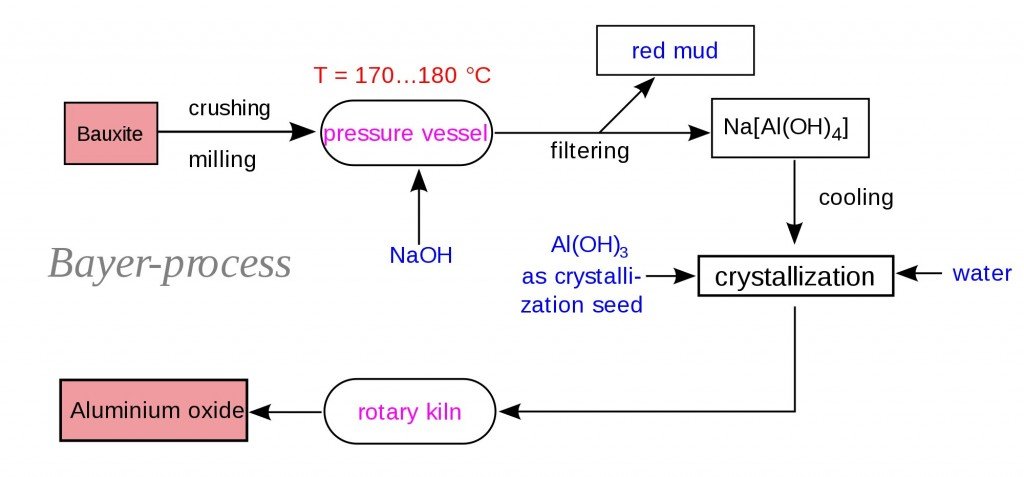
The slurry is then pumped into a settling tank. As the slurry rests in this tank, impurities that will not dissolve in the caustic soda settle to the bottom of the vessel. The residue (called “red mud”) that accumulates in the bottom of the tank consists of fine sand, iron oxide, and oxides of trace elements like titanium. After the impurities have settled out, the remaining liquid, which looks somewhat like coffee, is pumped through a series of cloth filters. The filters trap any fine particles of impurities that remain in the solution. This material is washed to recover alumina and caustic soda, which can be reused. The filtered liquid is pumped through a series of six-story-tall precipitation tanks. Seed crystals of alumina hydrate (alumina bonded to water molecules) are added through the top of each tank. The seed crystals grow as they settle through the liquid and dissolved alumina attaches to them. The crystals precipitate and sink to the bottom of the tank, where they are removed. After washing, they are transferred to a kiln for calcining (heating to release the water molecules that are chemically bonded to the alumina molecules). A screw conveyor moves a continuous stream of crystals into a rotating, cylindrical kiln that is tilted to allow gravity to move the material through it. A temperature of 1,100° C eliminates the water molecules, leaving anhydrous (waterless) alumina crystals. After leaving the kiln, the crystals pass through a cooler.
Hall-Heroult Process
The smelting of alumina into metallic aluminum takes place in a steel vat called a reduction pot. The bottom of the pot is lined with carbon, which acts as one electrode of the system. The opposite electrodes consist of a set of carbon rods suspended above the pot; they are lowered into an electrolyte solution and held about 3.8 cm above the surface of the molten aluminum that accumulates on the floor of the pot. Reduction pots are arranged in rows potlines consisting of 50-200 pots connected in series to form an electric circuit. Each potline can produce 60,000-100,000 metric tons of aluminum per year. A typical smelting plant consists of two or three potlines. Within the reduction pots, alumina crystals are dissolved in molten cryolite at a temperature of 960-970° C to form an electrolyte solution that will conduct electricity from the carbon rods to the carbon-lined bed of the pot. A direct current of 4-6 volts and 100,000-230,000 amperes is passed through the solution. The resulting reaction breaks the bonds between the aluminum and oxygen atoms in the alumina molecules. The oxygen released is attracted to the carbon rods, where it forms carbon dioxide. The freed aluminum atoms settle to the bottom of the pot as molten metal.
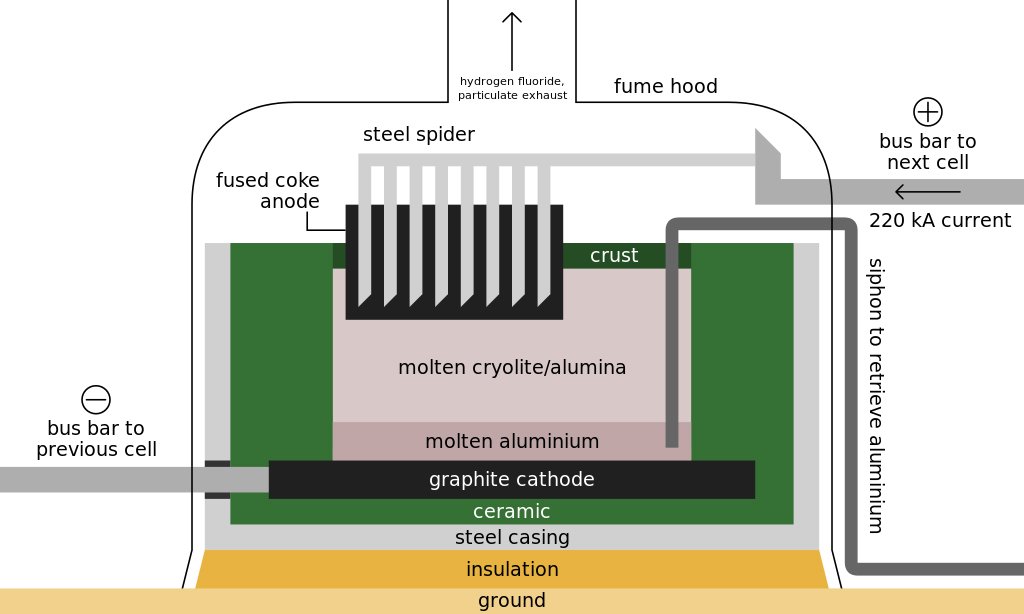
The smelting process is a continuous one, with more alumina being added to the cryolite solution to replace the decomposed compound. A constant electric current is thus maintained. Heat generated by the flow of electricity at the bottom electrode keeps the contents of the pot in a liquid state, but a crust tends to form atop the molten electrolyte. Periodically, the crust is broken to allow more alumina to be added for processing. The pure molten aluminum accumulates at the bottom of the pot and is gradually siphoned off. The pots are operated 24 hours a day, seven days a week. A crucible is moved down the potline, collecting 4,000 kg of molten aluminum, which is 99.8% pure. The metal is then transferred to a holding furnace and cast as ingots. One common technique consists of pouring the molten aluminum into a long, horizontal mold. As the metal moves through the mold, the exterior is cooled with water, causing the aluminum to solidify. The solid shaft emerges from the far end of the mold, where it is sawed at appropriate intervals to form ingots of the desired length. Like the smelting process itself, this casting process is also continuous. The aluminum is then collected and shipped off to various market players for their individual manufacturing purposes.
Also Read: Is It Possible To Convert Alloys To Their Base Metals?
How well do you understand the article above!
