Table of Contents (click to expand)
Carbon fiber is a graphite fiber that is extremely lightweight and strong. It is made by drawing the fiber into long strands, heating to a high temperature, and carbonizing to expel the non-carbon atoms. The surface is then treated and the fiber is ready to be used in various products.
Carbon fiber is a kind of polymer that is sometimes referred to as graphite fiber. It’s a solid material and is extremely lightweight in comparison to its strength. Carbon fiber is incredibly strong—five times stronger than steel and twice as rigid! The best part is, even though it is stronger and stiffer than steel, it is significantly lighter in weight than steel. These qualities make carbon fiber the most preferred element in many industries for the manufacturing of its products. Now, let’s take a look at the classification and raw materials of carbon fiber.
Classification And Raw Materials
The ranking of carbon fiber is based on the tensile modulus of the fiber. Tensile modulus can be defined as the measure of the amount of pulling force exerted on an object before it breaks. The unit used to measure the tensile modulus of an object is psi (pounds of force per square inch). Carbon fibers classified as low modulus have a tensile modulus below 34.8 million psi. The other classifications of carbon fibers based on their tensile modulus include standard modulus, intermediate modulus, high modulus, and ultrahigh modulus. Ultrahigh tensile modulus carbon fibers have a tensile modulus of 72.5-145 million psi. In comparison, steel has a tensile modulus of about 29 million psi. Thus, the most durable form of carbon fiber is about five times stronger than steel.
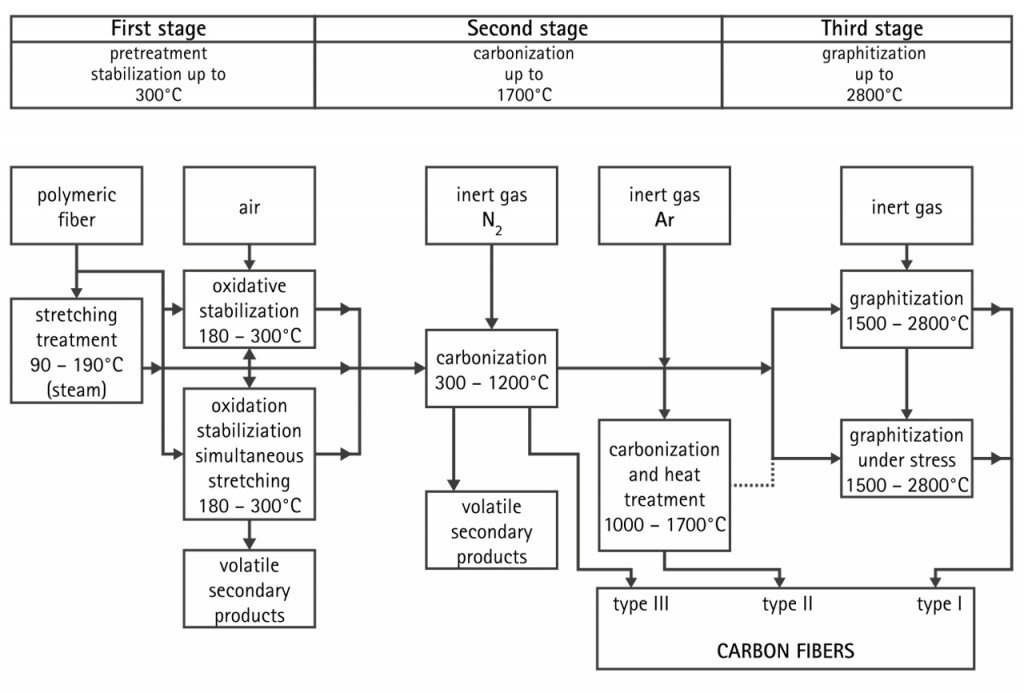
The raw material used to make carbon fiber is called the precursor. 90% of the carbon fibers produced are made from polyacrylonitrile. The remaining 10% is made from rayon or petroleum pitch. All of these materials are organic polymers. The characterization of organic polymers is formed by a long string of molecules bound together by carbon molecules. During the manufacturing process, certain gases and liquids are used. Some of these elements react with the fiber to bring about a specific effect. Other materials are designed not to respond or to prevent certain reactions with the fiber. As with the precursors, the exact compositions of many of these process materials are considered trade secrets.
Also Read: Graphene: The Material That’s Going To Change The Future
Manufacturing Process
The process of making carbon fiber is quite unique, as it is part mechanical and part chemical. The precursor is drawn into long strands heated to a very high temperature without allowing them to come in contact with oxygen. Without oxygen, the fiber cannot burn. Instead, the high temperature causes the atoms in the fiber to vibrate violently until most of the non-carbon atoms are expelled. This process is called carbonization and leaves a long, tightly woven fiber. The fibers are then coated to protect them from damage during winding or weaving. The coated fibers are wound onto cylinders called bobbins.
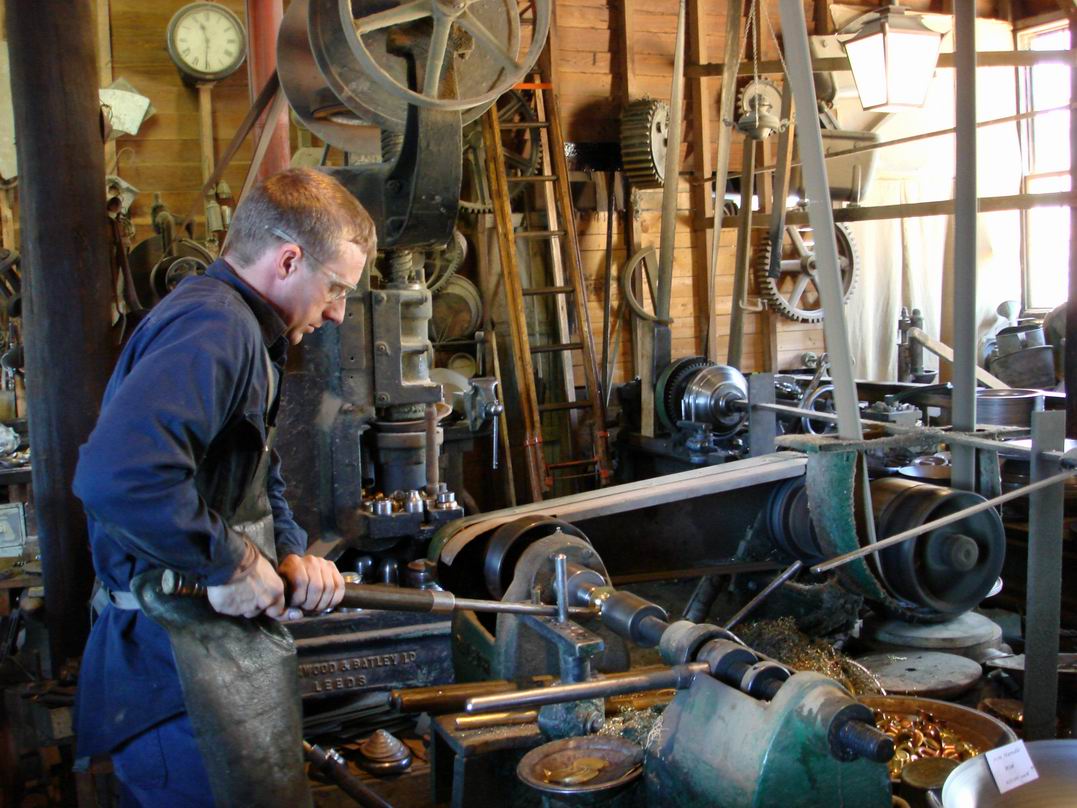
The first process is known as the spinning process. Acrylonitrile plastic powder is mixed with another plastic, such as methyl acrylate or methyl methacrylate, and is reacted with a catalyst in a conventional suspension or solution polymerization process to form a polyacrylonitrile plastic. The plastic is then spun into fibers using one of several different methods. In one particular method, specific chemicals are pumped through tiny jets into a chemical bath where the plastic coagulates and solidifies into fibers. The spinning step is important, as it helps in directing the internal atomic structure of the fibers. The fibers are then washed and stretched to the desired fiber diameter.
The subsequent step is the stabilizing of the fiber. The stabilizing process is done because the fibers need to be chemically altered to convert their linear atomic bonding to a more thermally stable ladder bonding. The stabilization process is done by heating the fiber in the air at 200-300°C for 30-120 minutes. This ensures that the fibers pick up oxygen molecules from the air and rearrange their atomic bonding pattern. Once the fibers are stabilized, we move into the carbonizing process, where they are heated to a temperature of about 1,000-3,000° C for several minutes in a furnace filled with a gas mixture that does not contain oxygen. This lack of oxygen prevents the fibers from burning in the very high temperatures. The gas pressure inside the furnace is kept higher than the outside air pressure and the points where the fibers enter and exit the furnace are sealed to prevent any oxygen from entering. The heating process removes the non-carbon atoms. As the non-carbon atoms are expelled, the remaining carbon atoms form tightly bonded carbon crystals that are aligned more or less parallel to the long axis of the fiber. In some processes, two furnaces operating at two different temperatures are used to control the rate of de-heating during the carbonization phase.
After the carbonizing comes the treating of the surface. The surface must be treated, as it is not ready to be bound with other epoxy composites. The addition of oxygen atoms to the surface of the fiber provides better chemical bonding properties. Oxidation can be achieved by immersing the fibers in various gases, such as air, carbon dioxide or ozone, or multiple liquids, such as sodium hypochlorite or nitric acid. The fibers can also be coated electrolytically by making the fibers the positive terminal in a bath filled with various electrically conductive materials. The surface treatment process must be carefully controlled to avoid the formation of tiny surface defects, such as pits, which could cause fiber failure. After the fibers are treated, they’re ready for the final process, which is the resizing. Coating materials are chosen that are compatible with the adhesive used to form composite materials. Typical coating materials include epoxy, polyester, nylon, urethane, and others. After this, they are packaged and shipped off to various manufacturers so the carbon fiber can be integrated into a wide range of products.
Also Read: What Is Modal Fabric?
How well do you understand the article above!
