Table of Contents (click to expand)
Tunnels are built by a variety of methods, depending on the type of tunnel, its purpose, and the materials it is made of. The most common method is to build a tunnel on the ground and then place it underwater. This is done by constructing segments of the tunnel on the ground and then sealing them with bulkheads to make them float. The segments are then placed in a long, narrow trench that has been dredged and graded prior to construction.
Voyages, while beautiful to undertake, can often be life-threatening. A ship or a ferry is vulnerable to being swallowed whole by high tides and ravenous storms. In 1954, five ferries dissolved into Tsugaru Strait, the body of water between Hokkaido Island and Aomori Prefecture, after it was possessed by typhoons.
The public was incensed. Building a bridge was not an alternative either, for the tempestuous winds would simply tear it down. The safest alternative was also the most mind-boggling… to build a tunnel under the water. Even so, they did it. In 1998, the government didn’t just build any underwater tunnel, but the deepest and longest of its kind. The Seikan Tunnel lies 140m below the seabed and spans almost 54km in length! The question is, of course, how in the world are these engineering marvels constructed with all the mud and water torrenting in from even the tiniest of punctures?
The Tunneling Shield
The world’s first underwater tunnel was built under the river Thames, which drifts through London. In the early 19th century, London was the linchpin of trade in Europe and much of the rest of the world. The ports were congested with ships carrying coal and other goods and the roads were replete with horse-drawn vehicles. The congestion was perturbing, especially since industrialism was on the rise. They needed a way to increase their rate of trade and travel without increasing the floating traffic.
Back then, the idea of building a tunnel underwater was obviously outrageous; it was the stuff of utopian prophecies. However, it also was, the engineers realized, the most efficient solution. There were risks, of course: meters below, mud and water driven by pressure could penetrate through crevices and collapse the entire tunnel, which would obviously be disastrous.
However, in 1818, Marc Brunel, known as one of England’s most brilliant engineers, developed an ingenious device that could tunnel through the seabed without allowing any mud or water to seep in! His construction was the stuff of genius. He used what is now called a ‘tunnel shield’, a 40-foot submarine protected by a wall of steel and bricks around 3 feet thick.
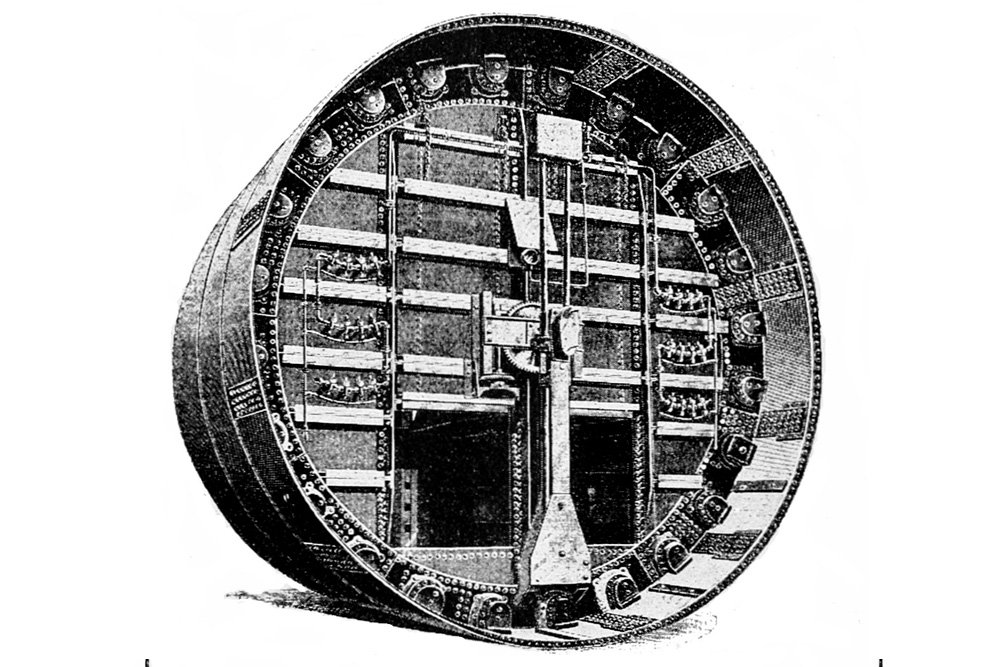
The Thames Tunnel between Wapping and Rotherhithe wasn’t excavated by a large drilling machine, but by people literally chipping at rocks and sand. As the shield moved forward, workers in the front, who were exposed through small cavities, would dig, while the people behind would line bricks along the tunnel that had just come into being. The workers had to develop two outlets, one for disposing of mud and sand, and another for water.
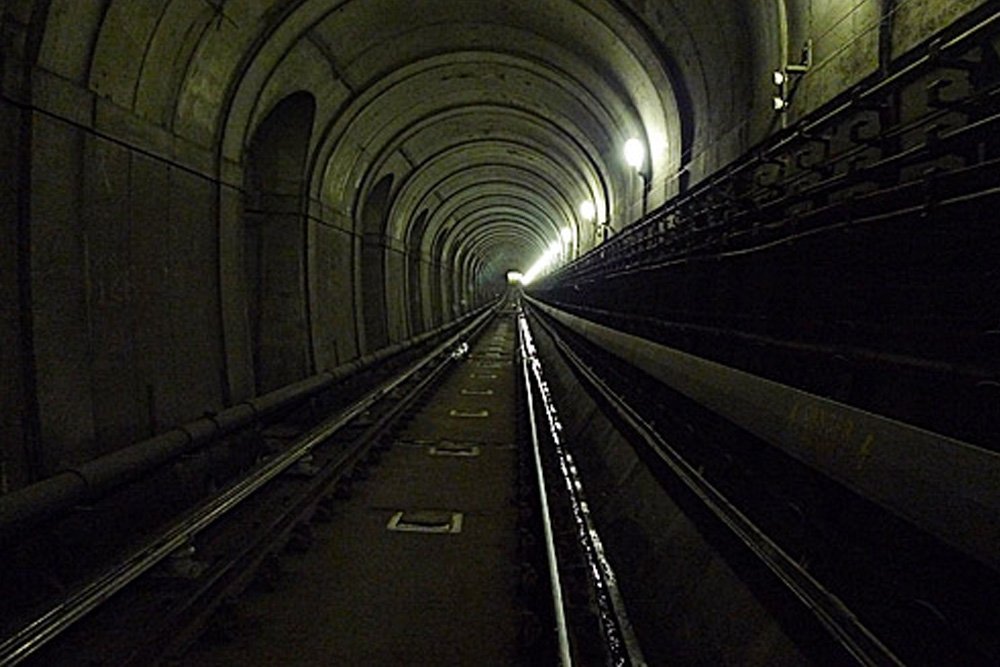
What was predicted to take only 3 years actually took around 18. Finally, the bricks were fortified by concrete and the development of a tunnel capable of bearing horse-drawn vehicles – and later trains – was finally complete. The tunnel is still a crucial part of London’s Overground railway network. For a brief period, it was deemed to be the 8th wonder of the world.
Also Read: How Do Breakwaters Protect The Shoreline?
The Prefabricated Tunnel And ‘Moles’
However, rather than building a tunnel as it is simultaneously dug, one can first construct a tunnel on the ground and then later place it underwater.
Such a tunnel is not built in its entirety, but rather in segments. The concrete segments are sealed with bulkheads to ensure they float. With the help of additional weights, the segments are forced to sink and are placed in a long, narrow cavity that runs the length of the tunnel to be built. The cavity is developed by dredging and grading the trench prior to the construction of the segments. Each segment is then joined to form the tunnel. The water between the joints is pumped out hydraulically and the tunnel is water sealed. All that is left is a long, exquisite tunnel and a team of delighted engineers.
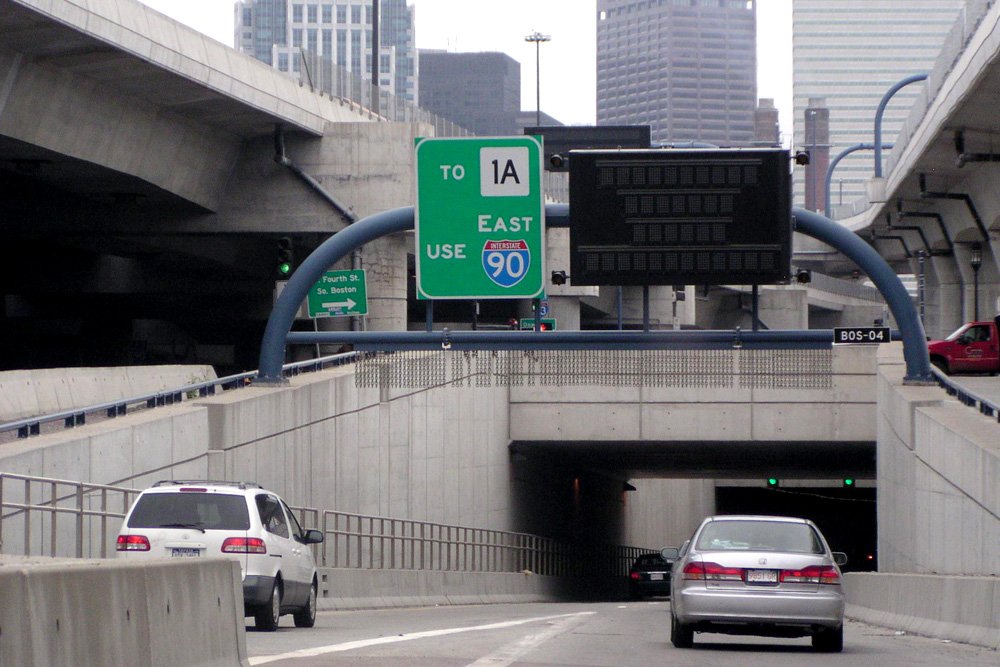
The Ted Williams tunnel, which connects the southern part of Boston and Logan Airport, was built in this fashion. Twelve segments, each 325 feet long, were joined to form the tunnel. Even more astonishing is the fact that each of them housed already fully-constructed roads!
While this technique is cost-effective, it does have many disadvantages. First, engineers are required to be extremely careful when sinking the segments, as even a slight misalignment can result in devastating consequences. Second, while immersed tunnels are built under a trench, there is the possibility that a few segments facing the water might be exposed. These openings could result in horrific accidents if struck by sunken ships or anchors. And third, obviously, is the detrimental effects of digging on the channel’s bed, and therefore, the environment and ecosystem.
The most convenient method, however, is to use a drill, except that it must be gigantic. The Channel Tunnel connecting U.K. and northern France was built by monstrous machines called Tunnel Boring Machines (TBM). A TBM, also known as a ‘mole’, is a machine that excavates tunnels by cutting through rocks and strata with rapidly rotating blades.
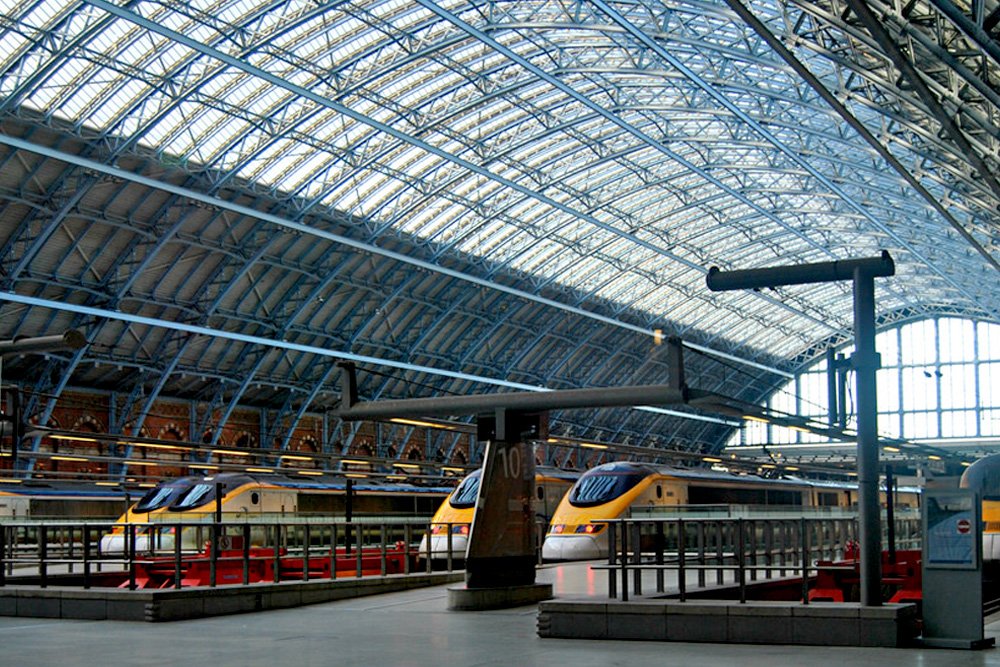
Of course, this convenience is expensive. Furthermore, a single machine, which costs some millions of dollars, is insufficient to build a tunnel by itself. The Channel Tunnel required 11 of them to build. However, while the preferred method of building a tunnel does rely on convenience, the speed of construction and expenditure, the most important factor remains the nature of the soil that must be penetrated. As a result, no technique can be crowned to be the absolute best.
Also Read: What Are Canal Locks And How Do They Work?
How well do you understand the article above!
